Printed Rapid Prototype Service
For Georgia local printed plastic rapid prototyping services WhiteLight Design and Product QuickStart is your fast response solution. Rapid Prototyping production can product parts in a few hours or days. Our Product Quickstart Prototype Shop in Lawrenceville, Atlanta, GA has the experience, access to equipment, materials knowledge and integrity to aide you in producing a tangible preview of your invention or ready for the store shelf product design. We utilize rapid prototyping technologies, including SLA-SLS-FDM-RTV Cast Urethane and full rapid CNC machining. Wood, metal, plastic, carbon fiber or titanium if requested deliver prototypes of complete products, product components, or machined parts in 5-15 days, thereby saving you time and money. Either for an investors or a upcoming trade show, when deadlines and Speed to Market are important, our product prototype development services will rise to the challenge.
We utilize rapid prototyping technologies, including SLA-SLS-RTV – Cast Urethane and full rapid CNC machining. Wood, metal, plastic, carbon fiber or titanium if requested deliver prototypes of complete products, product components, or machined parts in 5-15 days, thereby saving you time and money.
Rapid Prototyping (RP)
The RP additive process options main differences is in the way the layers are built to create the part. The SLA is a laying liquid resin thermosets that are cured with UV light activated photopolymers. SLS and FDM are melting, softening or fusing material to produce the layers.
SLA Stereolithography
SLA uses a focused laser beam over a vat of liquid photo polymer resin. As the laser draws the layer, the photo polymer changes from a liquid to a solid. When the cross-section is solidified, another layer of liquid photopolymer covers the surface of the previous layer and laser solidifies this layer, and so on. When the part is finished, it is removed from the vat and cleaned of its support structures and excess resin. Then it must go through a final post-curing process. There are several resins option available. Maximum dimensions 20″x20″x20″.
SLS – Selective laser sintering
Selective laser sintering (SLS) is another focused laser beam technology which draws the cross-section of the part being built on a layer of powder. As the laser draws, the heat of the laser fused the particles of powder together. At the end of the cross-section, another layer of powder is applied to the surface and then it too is drawn and fused, adhering to the layer below. When the part is finished, the unsolidified powder is removed from the part. The SLS process can use several different materials which offer the closest mechanical representation of an injection molded part including glass filled for extra rigidity, strength, heat and & chemically resistant. Currently materials available for functional testing elastomeric, polystyrene, sand form patterns, rapid steel and copper polyamide. Typically SLS parts are not used for appearance quality parts based on the granular surface finish and the finishing work necessary to achieve appearance quality.
Maximum dimensions 10 x 12 x 16″
FDM – Fused Deposition Modeling
FDM Fusion Deposit Modeling excellent for Conceptual Models, Engineering Models, and Functional Testing Prototypes. This process uses an extrusion head to deposit a bead of material on a layer by layer platform contouring to the desired geometry. The most common material is ABS. or a medically approved grade of ABS Also used for investment casting molds. Maximum dimensions single build: ABS – 23″x19″x23″, Polycarbonate (PC) – 14″x16″x16″.
RTV
Rapid Thermal Vulcanization
RTV Molding or Cast Modeling is a low volume prototyping technique that can produce parts from soft to hard using soft urethane mold materials to cast urethane and or silicone plastics. These parts can simulate or appear just like injection molded plastic parts with similar surface finish, color, properties. RTV models are recommended when a client needs 10 – 20 units are the goal up to 100 units with multiple tools. This process consists of creating or SLA a master model pattern from which a core and cavity( two piece – clam shell) plywood box molds are cast with a rubber like urethane material. The molds are then used to gravity or vacuum feed to cast multiple parts of a desired product component. After molding, final clean-up and finishing is necessary. An RTV model program may consist of two to ten different part molds to build a product design. Materials include materials similar in materials properties to ABS, PE, PC Polycarbonate and Nylon. Maximum dimensions : 20″x20″x20″. Larger parts are achieved in sections glued together.
Rapid Prototyping – is great for Design Verification, our modelmaking and prototype services also include:
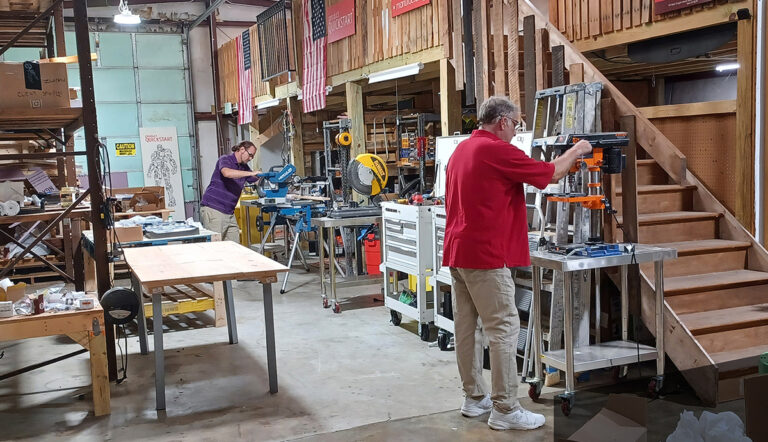
Our Lawrenceville Prototype shop is built to be flexible space with movable tools and project tables to serve as a small manufacturing cell.
We typically have to create the design and 3D CAD files or drawings before we can go to the shop or RFQ quote the parts or full assembly model. For questions or to schedule an initial consultation or request a Model Making or Prototype quotation please call us at (770) 277-7097. We will need to review your design – drawings, prototype or CAD information to provide a quotation. Remember—for product development prototyping services that won’t let you down, choose WhiteLight Design. We’re looking forward to working with you!
ASK WhiteLight Prototype Shop – General Questions: Willis Whiteside willis@whitelightdesign.com